Die chemische Industrie und die Düngemittelindustrie haben in den letzten vier Jahrzehnten auf großange-legte Ammoniakanlagen gesetzt, weil Größenvorteile niedrigere spezifische Bau- und Produktionskosten begünstigen.
Das Geschäftsmodell für diese größeren Anlagen beruhte teilweise auf der Tatsache, dass das nicht vor Ort verbrauchte Ammoniakprodukt exportiert werden konnte, was nach einfachen Transportmög-lichkeiten zu anderen Nutzern zu wirtschaftlich attraktiven Kosten verlangte. Zunehmende Sicherheitsbeden-ken beim Transport von chemischen Gefahrstoffen haben jedoch zu höheren Frachtkosten und Versiche-rungsprämien für den Transport von wasserfreiem Ammoniak geführt. Dies betrifft die meisten Kleinverbrau-cher von Ammoniak, die auf den Import von Ammoniak per Bahn, Schiff oder LKW angewiesen sind.
Eine machbare Alternative ist der Bau einer kleinen Ammoniakproduktionsanlage neben einer Verbrauchs-stelle, um somit die Transportrisiken und -kosten zu vermeiden. Konventionelle Anlagenkonzepte stehen vor technischen und wirtschaftlichen Herausforderungen bei Anlagen mit Kapazitäten von weniger als 600 ame-rikanischen Tonnen pro Tag (550 Tagestonnen). thyssenkrupp Industrial Solutions und Johnson Matthey sind dieses Problem angegangen und haben ein wirtschaftliches Konzept für kleinere Anlagen auf der Basis der gasbeheizten Reformertechnologie entwickelt.
Infolgedessen kann thyssenkrupp Industrial Solutions nun Anlagen mit Kapazitäten zwischen 270 und 550 Tagestonnen (300 bis 600 amerikanischen Tonnen pro Tag) anbieten und hält ein sofort umsetzbares Stan-dardkonzept für 360 amerikanische Tonnen pro Tag bereit. Diese Anlage verwendet einen gasbeheizten Reformer (GHR) und ein Druckwechseladsorptionssystem (PSA) im Front-End sowie einen Niederdruck-Synthesekreislauf im Back-End.
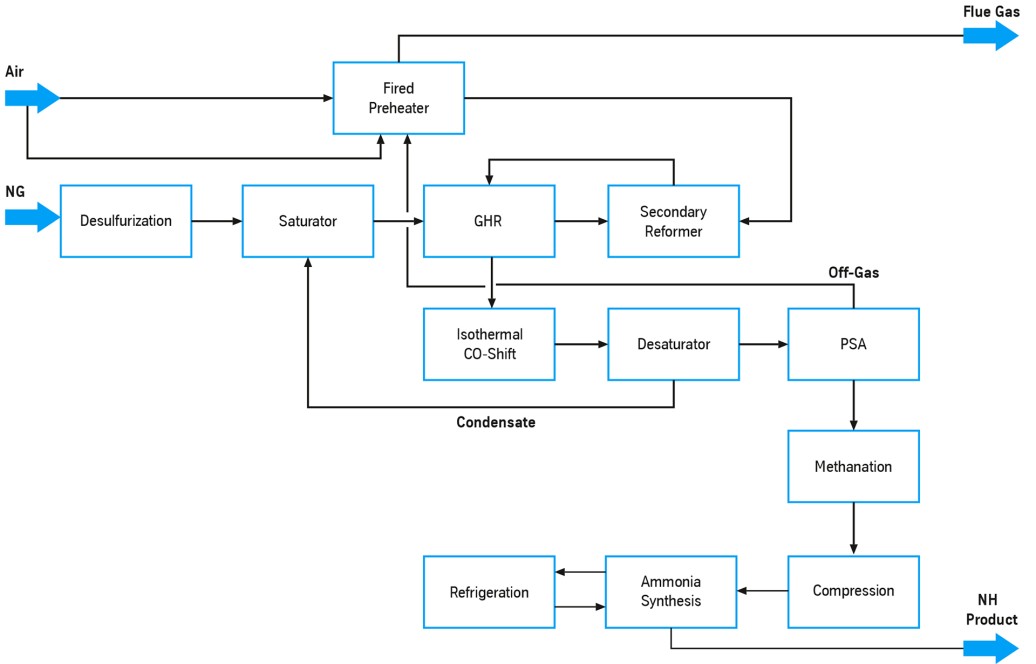