Die Kapazitäten chemischer Anlagen werden schon seit langer Zeit immer größer. Der Grund hierfür liegt in der Verringerung der spezifischen Produktionskosten durch Größenvorteile. Mehr denn jemals zuvor sieht sich der Anlagenbau vor die Herausforderung gestellt, diesen Vorteil zu nutzen und gleichzeitig weiterhin bewährte Technologien und Ausrüstungen zu verwenden.
Mit ihren Katalysatoren haben Uhde und Johnson Matthey diese Herausforderung angenommen und ein Verfahren entwickelt, das auf der vorhandenen Technologie beruht und Ammoniakanlagen nun ermöglicht, in sehr großen Kapazitäten zu produzieren. Dieses neue Verfahren (siehe Ablaufdiagramm) liefert eine Kapazität von 3.300 Tagestonnen unter Verwendung von erprobter und bewährter Ausrüstung. Es bildet auch die Grundlage für noch größere Anlagen (z. B. 4.000 bis 5.000 Tagestonnen).
Die erste auf diesem Verfahren basierende Anlage ist die SAFCO IV Ammoniakanlage in Al-Jubail, Saudi-Arabien, die 2006 in Betrieb gegangen ist. Mit einer Kapazität von 3.300 Tagestonnen ist sie bei weitem die größte Ammoniakanlage weltweit.
Technologische Highlights
- Bewährte Technologie, die bei mehreren aktiven Anlagen zum Einsatz kommt.
- Bewährte Katalysatoren auf Magnetit-Basis in allen Phasen des neuen Prozesses.
- Verbesserte Energieeffizienz.
- Eine hohe Konversionsrate im Hochdruck-Synthesekreislauf und reduzierte Produktionsanforderungen führen zu kleineren Rohrleitungsgrößen im Hochdruckkreislauf. Standardrohrleitungen können bei Kapazitäten von 4.000 Tagestonnen und mehr verwendet werden.
- Der Synthesegaskompressor einer Zweidruckanlage mit 3.300 Tagestonnen hat dieselbe Größe wie in herkömmlichen Ammoniakanlagen für 2.200 Tagestonnen; mehrere Referenzkompressoren sind derzeit in Betrieb.
- Es gibt keine großen Abweichungen von den herkömmlichen Prozessbedingungen.
Die wichtigste Innovation beim neuen Zweidruck-Ammoniakverfahren von Uhde ist eine zusätzliche Einmal-Ammoniaksynthese bei mittlerem Druck in Verbindung mit dem herkömmlichen Hochdruck-Ammoniaksynthesekreislauf wie folgt:
1. Die Einmal-Ammoniaksynthese umfasst die Kompression des Zusatzgases in einem zweistufigen Kompressor mit Zwischenkühler. Diese findet im Niederdruckgehäuse (LP-Gehäuse) des Synthesegaskompressors statt. Der Druck am Ansaugflansch des Kompressors beträgt ca. 110 bar. Bei diesem Druck erzeugt der zwischengekühlte Einmal-Konverter mit drei Katalysatorbetten ungefähr ein Drittel des gesamten Ammoniakausstoßes. Die Synthesegas-Ammoniak-Mischung, die diesen Konverter verlässt, wird gekühlt, wobei 85 % des hergestellten Ammoniaks als Flüssigkeit vom Gas getrennt wird.
2. Das verbleibende Synthesegas wird dann im Hochdruckgehäuse des Synthesegaskompressors auf den Betriebsdruck des Ammoniaksynthesekreislaufs (bis zu 210 bar) komprimiert. Da das Synthesegas abgekühlt worden ist, kann das Hochdruckgehäuse mit einer viel geringeren Temperatur als beim herkömmlichen Ammoniakverfahren arbeiten. Der Druck für den Hochdruck-Synthesekreislauf wird durch eine Kombination aus dem Druck im gekühlten zweiten Gehäuse des Synthesegaskompressors und einem leicht erhöhten Front-End-Druck erzielt. Bei diesem herkömmlichen Ammoniaksynthese-Kreislauf werden die verbleibenden zwei Drittel des Gesamtammoniaks produziert.
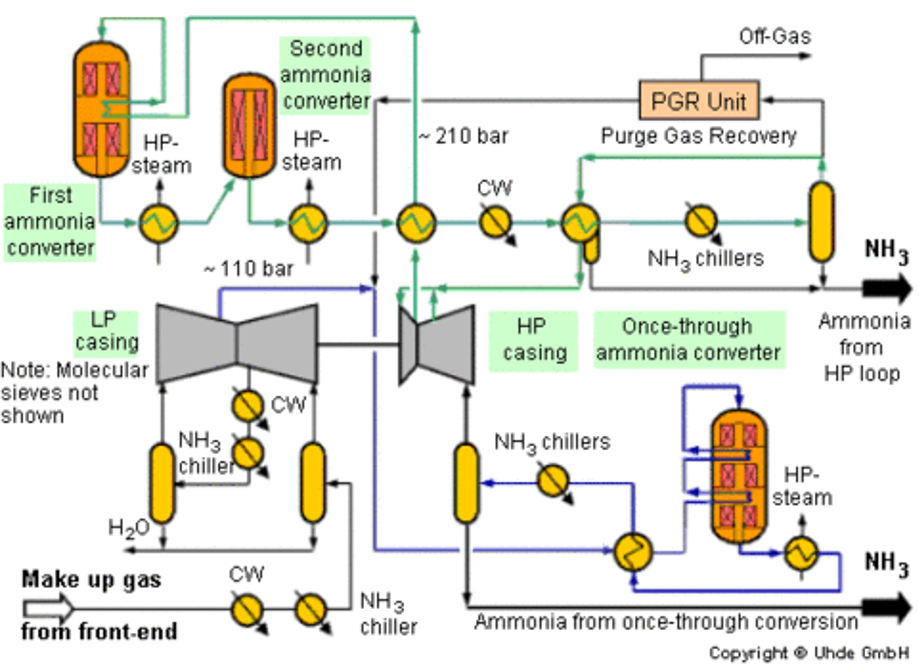