Ammoniak-Düngemittelanlagen von thyssenkrupp
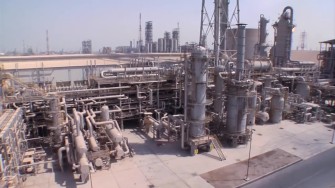
thyssenkrupp Industrial Solutions entwickelt und baut seit ca. 90 Jahren Stickstoffdüngemittelanlagen auf Basis der Technologie von Uhde und ist ein führender Anbieter in diesem Bereich mit einer langen Liste von Referenzen.
Wir sind in der Lage, Projekte zu einem allumfassenden Pauschalbetrag auf EPC-Basis abzuwickeln und können auf viele bewährte Referenzanlagen von Weltrang mit Kapazitäten von 600 bis 3300 Tagestonnen verweisen. Unser Name steht für erstklassige Technologien, die kontinuierlich verbessert werden, sowie für ausgezeichnetes Management von Großprojekten, moderne internationale Beschaffungsstrategien auf einem globalen Markt und jahrzehntelange Erfahrung in allen Erdteilen. Unser Unternehmen ist somit in der Lage, seinen Kunden auf der ganzen Welt optimale Lösungen für maximale Kosteneffizienz, Zuverlässigkeit und Umweltverträglichkeit zu bieten. Unsere Kunden sind das Who is Who der Düngemittelindustrie.
thyssenkrupp Industrial Solutions liefert Anlagen für die Dampfreformierung von Erdgas oder Naphta Kohlevergasung, Wasserstoffverfahren aund Elektrolyse und bietet eine Palette von Produkten, wie beispielsweise Harnstoffschmelze, DEF, Harnstoffgranulat, AN Prills, Salpetersäure, AN/UAN Lösungen, Phosphatdünger und Methanol. Wir bieten Ammoniakanlagekapazitäten von 200 bis 500 Tagestonnen (kleine Ammoniakanlagen) sowie von 500 bis 4.500 Tagestonnen (große Uhde-Ammoniakanlagen). Mit diesen Referenzen zählt thyssenkrupp zu einem der marktführenden Unternehmen in diesem Geschäftsbereich.
Übersicht
Die Dampfreformierung von Kohlenwasserstoffen ist ein etabliertes Verfahren zur Erzeugung von Synthesegas und Wasserstoff etc. Das Dampfreformierungsverfahren umfasst die Hochtemperaturreaktion von Methan oder höheren Kohlenwasserstoffen mithilfe eines Katalysators zur Erzeugung von Wasserstoff und Kohlenmonoxid gemäß der folgenden Reaktionsgleichung:
CnH2n+2 + nH2O = nCO + (2n +1)H2
Die Reformierung findet in Rohren statt, die mit einem Katalysator ausgestattet und in gasbefeuerten Dampfreformern vertikal angeordnet sind. Es kommt ein auf einem Traggerüst angebrachter Nickelkatalysator zum Einsatz. Die Betriebsbedingungen des Dampfreformers variieren in Abhängigkeit von der Anwendung in einem Temperaturbereich zwischen 740°C und 950°C und Drücken bis zu 50 bar. Diese sehr unterschiedlichen Betriebsbedingungen erfordern ein vielseitiges Reformerkonzept.
Das urheberrechtlich geschützte Reformerkonzept von Uhde hat in den vergangenen Jahrzehnten die Bewährungsprobe in Sachen Leistung bestanden und dabei die Anforderungen der verschiedenen Anwendungen erfüllt. Weiterentwicklungen in allen kritischen Bereichen haben zu einem hohen Maß an Rundum-Zuverlässigkeit geführt. Infolgedessen nutzen viele Kunden die Reformertechnologie von Uhde.
Technologische Highlights
- Das einzigartige Kaltauslass-Verteilersystem von thyssenkrupp Industrial Solutions steht für maximale Zuverlässigkeit
- Optimale Wärmeverteilung durch Deckenbefeuerung mit modernen Brennern (geringe NOx-Emissionen garantiert)
- Höhere Effizienz im Vergleich mit seitlich befeuerten Reformern
- Einsatz modernster Reformerrohrmaterialien aufgrund der Erfahrungen, die thyssenkrupp Industrial Solutions in vielen Referenzanlagen gewonnen hat
- Modulkonzept für einfachen Transport und eine wirtschaftliche Bauweise
- Das Reformerkonzept sorgt für einfachen Zugang und benötigt nur ein Mindestmaß an Grundfläche
- Reduzierung von Wartungsarbeiten auf ein außergewöhnlich niedriges Niveau:
- Deckenbefeuerung erfordert eine viel kleinere Anzahl von Brennern als seitliche Befeuerung
- Die Kastenbauweise mit flachen Wänden ermöglicht standardisierte feuerfeste Auskleidungen mit Ziegelsteinen oder Keramikfasern
- Selbst bei großen Kapazitäten wird nur eine Brennkammer benötigt
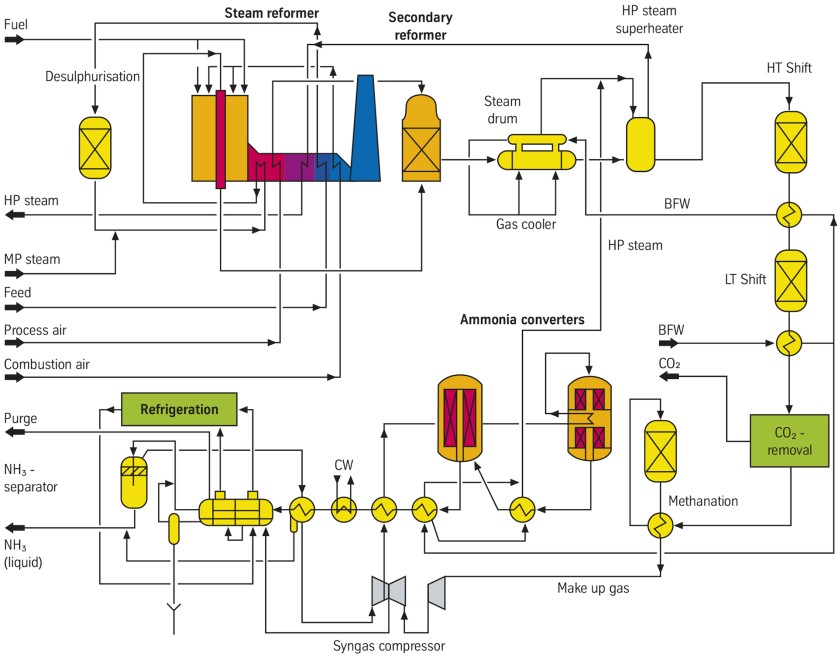
Verfahren und Konzept für Ammoniakanlagen von Uhde basieren auf zuverlässigen und bewährten Prozessschritten. Die wichtigsten Merkmale sind ein deckenbefeuerter Primärreformer mit einem Kaltauslass-Verteilersystem, ein Sekundärreformer mit einem Umlauf-Wirbelbrenner und drei Katalysatorbetten auf Magnetitbasis nach dem Radialflussprinzip zur Wärmeaustauschsynthese mit einem oder zwei Synthesekonvertern.
Der Rohstoff (beispielsweise Erdgas) wird entschwefelt, mit Dampf vermischt und mit Nickelkatalysatoren bei etwa 40 bar und 800°C im Primärreformer in Synthesegas umgewandelt. Der Dampfreformer von Uhde ist ein deckenbefeuerter Reformer mit Rohren aus einem im Schleudergussverfahren hergestellten legierten Stahl und einem urheberrechtlich geschützten Kaltauslass-Verteilersystem zur Verbesserung der Zuverlässigkeit.
Das Prozessgas, das den Primärreformer verlässt, gelangt in den Sekundärreformer, wo dem Synthesegas über ein spezielles Düsensystem, das für eine perfekte Mischung aus Luft und Gas sorgt, Prozessluft zugeführt wird. Die folgende Hochdruck-Dampferzeugung und Überhitzung ermöglichen eine maximale Prozesswärmenutzung, wodurch eine optimale Energieeffizienz erreicht wird. Seit seiner Einführung im Jahre 1968 hat sich der Sekundärreformer von Uhde als zuverlässiges Gerät mit langer Lebensdauer erwiesen.
Kohlenmonoxid wird in der HT- und LT-Schicht über Standardkatalysatoren zu Kohlendioxid umgewandelt. Kohlendioxid wird in einer Abluftreinigungsanlage entfernt, bei der üblicherweise das BASF-OASE- oder das UOP-Benfield-Verfahren zum Einsatz kommt. Verbleibende Kohlenoxide werden durch katalytische Methanisierung im ppm-Spurenbereich zu Methan rückkonvertiert.
Das Ablaufdiagramm einer Uhde-Ammoniakanlage zeigt die herkömmliche Reihenfolge der Prozessschritte, die die Basis der meisten heutzutage angewandten Ammoniakverfahren bilden. Eine genauere Überprüfung der Fakten und Zahlen zeigt jedoch, dass das, was eine konventionelle Aufstellung zu sein scheint, tatsächlich ein hochmodernes Ammoniakanlagenkonzept ist. Der Gesamtverbrauch (Rohstoff + Treibstoff + Strom) pro Tonne hergestellten Ammoniaks liegt im Bereich zwischen 6,6 bis 7,2 Gcal (27,6 bis 30,1 GJ), je nach örtlichen Gegebenheiten (z. B. Temperatur des Kühlwassers) und projektspezifischen Anforderungen (wie beispielsweise Erdgaspreis usw.).
In folgenden Prozessbereichen wurden wesentliche Änderungen vorgenommen, um diese Werte zu erzielen:
- Dampfreformierungsanlage einschließlich Abwärmerückgewinnungssystem;
- CO2-Abscheidungsanlage;
- Ammoniaksyntheseanlage.
Das neue Ammoniakanlagenkonzept für 300 bis 600 amerikanische Ton-nen pro Tag von thyssenkrupp Industrial Solutions und Johnson Matthey’s
Die chemische Industrie und die Düngemittelindustrie haben in den letzten vier Jahrzehnten auf großange-legte Ammoniakanlagen gesetzt, weil Größenvorteile niedrigere spezifische Bau- und Produktionskosten begünstigen. Das Geschäftsmodell für diese größeren Anlagen beruhte teilweise auf der Tatsache, dass das nicht vor Ort verbrauchte Ammoniakprodukt exportiert werden konnte, was nach einfachen Transportmög-lichkeiten zu anderen Nutzern zu wirtschaftlich attraktiven Kosten verlangte. Zunehmende Sicherheitsbeden-ken beim Transport von chemischen Gefahrstoffen haben jedoch zu höheren Frachtkosten und Versiche-rungsprämien für den Transport von wasserfreiem Ammoniak geführt. Dies betrifft die meisten Kleinverbrau-cher von Ammoniak, die auf den Import von Ammoniak per Bahn, Schiff oder LKW angewiesen sind.
Eine machbare Alternative ist der Bau einer kleinen Ammoniakproduktionsanlage neben einer Verbrauchs-stelle, um somit die Transportrisiken und -kosten zu vermeiden. Konventionelle Anlagenkonzepte stehen vor technischen und wirtschaftlichen Herausforderungen bei Anlagen mit Kapazitäten von weniger als 600 ame-rikanischen Tonnen pro Tag (550 Tagestonnen). thyssenkrupp Industrial Solutions und Johnson Matthey sind dieses Problem angegangen und haben ein wirtschaftliches Konzept für kleinere Anlagen auf der Basis der gasbeheizten Reformertechnologie entwickelt.
Infolgedessen kann thyssenkrupp Industrial Solutions nun Anlagen mit Kapazitäten zwischen 270 und 550 Tagestonnen (300 bis 600 amerikanischen Tonnen pro Tag) anbieten und hält ein sofort umsetzbares Stan-dardkonzept für 360 amerikanische Tonnen pro Tag bereit. Diese Anlage verwendet einen gasbeheizten Reformer (GHR) und ein Druckwechseladsorptionssystem (PSA) im Front-End sowie einen Niederdruck-Synthesekreislauf im Back-End.
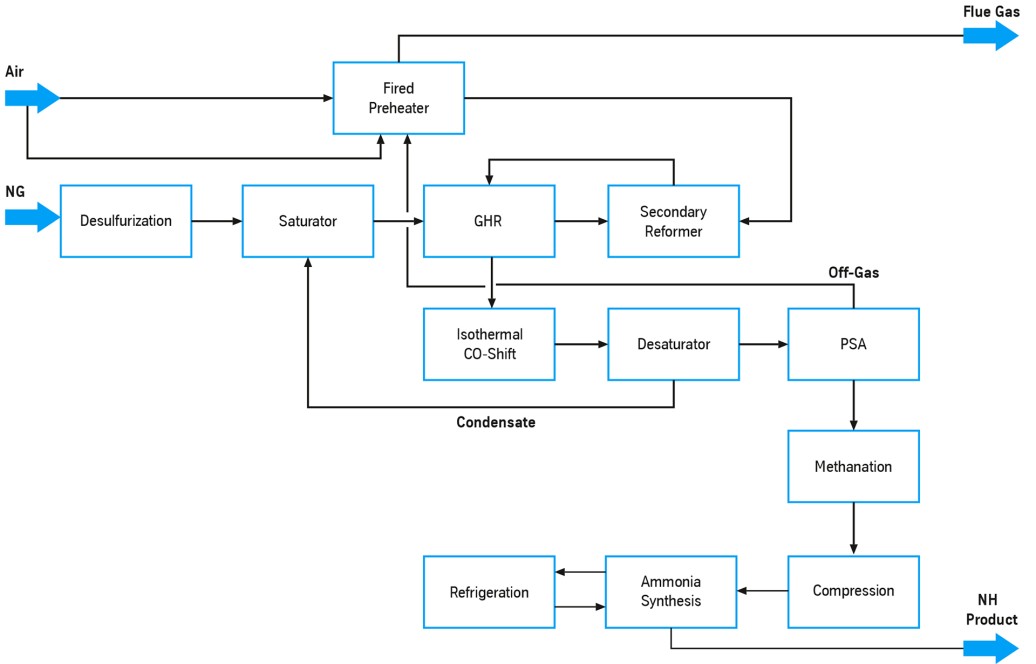
Sonderlösungen für Ammoniakanlagen, die Ihre Anforderungen erfüllen
Die hier vorgestellte Technologie konzentriert sich auf die Ammoniakproduktion aus der Dampfreformierung von Erdgas. Natürlich bieten wir Ihnen auch andere Technologien und Verfahren für andere Rohstoffe zur Produktion von Ammoniak an, wie beispielsweise:
- Autotherme Reformierung von Erdgas
- Naphtha-Reformierung
- Ammoniakherstellung mit Wasserstoff aus anderen Quellen, wie z. B. Wasserelektrolyse, Raffinerie-abgas usw.
Wir haben Lösungen für viele weitere Anforderungen, die sich im Rahmen von Ammoniakanlageprojekten ergeben, wie beispielsweise:
- Abscheidung von Schwefel aus Erdgas zum Schwefelexport
- Erhöhung des CO2-Exports an eine Harnstoff-Anlage oder CO2-Rückgewinnung aus Rauchgas
- besondere Anforderungen an die Abwasserbehandlung
- Ammoniaklagertanks
- u.v.m.
Wenden Sie sich an uns - wir sprechen gerne mit Ihnen über Ihre Anforderungen.
thyssenkrupp Industrial Solutions - Technologieservice
Kontinuierliche Verbesserung mit Hightech-Lösungen
Möchten Sie, dass Ihre Anlage dauerhaft mit höchstmöglicher Effizienz und höchsten Sicherheitsstandards arbeitet, und zwar nicht nur zu Beginn sondern während ihrer gesamten Lebensdauer?
Als Technologieführer mit rund 90 Jahren Erfahrung im Düngemittelgeschäft ist thyssenkrupp Industrial Solutions ihr ständiger Begleiter auf dem gesamten Lebensweg Ihrer Anlage.
Wer wir sind
Als professioneller Dienstleister für die Ammoniak- und Harnstoffindustrie bieten wir Ihnen ein umfassendes Serviceportfolio für eine kontinuierliche Verbesserung ihrer Anlage in Bezug auf einen möglichst geringen Stromverbrauch, erhöhte Kapazitäten, Verfügbarkeit und Sicherheit der Anlage sowie die Qualität der Produkte, um Sie auf Ihrem Weg zum „Branchenprimus“ aktiv zu unterstützen.
Was wir bieten
Neben unseren Dienstleistungen in den Bereichen Engineering, Betrieb und Wartung, Inspektion und Reparatur, Consulting und Analysen, Problembehebung und Ausbildung können wir Sie mit folgenden Services unterstützen:
Modernisierungen:
Auf der Grundlage unserer umfangreichen Erfahrung in der Konzeptionierung, dem Bau und der Inbetriebnahme neuer Anlagen hat thyssenkrupp Industrial Solutions eine breit angelegte Strategie zur Modernisierung von Ammoniak- und Harnstoffanlagen entwickelt, um die Anforderungen und Ziele unserer Kunden zu erfüllen, wie beispielsweise:
- Verbesserung der jährlichen Produktionsleistung
- Verbesserung der Energieeffizienz
- Verlängerung der verbleibenden Lebensdauer
- Verbesserung der Zuverlässigkeit der Anlage
- Reduktion von Emissionen
Engineering und Lieferung von Ausrüstung und Ersatzteilen:
Wenn Sie sich für thyssenkrupp Industrial Solutions als Lieferant Ihrer Ausrüstung entscheiden, profitieren Sie von der globalen Beschaffungsstruktur eines internationalen EPC-Auftragnehmers. Durch die Kombination von Engineering- und Beschaffungssachkenntnis beim Kauf von Equipment bieten wir unseren Kunden ein umfassendes Servicepaket, einschließlich Gewährleistung für Mechanik und Leistung sowie Inbetriebnahmedienstleistungen für die gelieferten Maschinen und Anlagen.
Austausch von Ammoniaksynthesekatalysatoren & Kartuschen:
Aufgrund der hohen Komplexität beim Austausch von Katalysatoren und Kartuschen im Ammoniakkonverter bieten wir unseren Kunden ein Full-Service-Paket. Als Generalunternehmer gewährleistet tkIS nicht nur eine kompetente Projektabwicklung und einen Festpreis für den Austausch von Katalysator und Kartusche unter Beachtung des festgelegten Zeitrahmens, sondern garantiert auch die Zuverlässigkeit der Leistung nach Wiederhochfahren der Anlage.
Das Full-Service-Paket für den Austausch von Katalysator und Kartusche in einem Ammoniakkonverter umfasst Folgendes:
- Projektmanagement einschließlich Bauleitung
- Verfahrens- und Arbeitsanweisungen
- Überwachung aller Arbeitsschritte
- Inspektionsdienstleistungen
- Lieferung von Katalysatoren, Kartuschen, Ersatzteilen und Werkzeugen
- Mechanische Arbeiten
- Katalysatorhandling
- Überwachung der Inbetriebnahme
- Leistungsoptimierung